How imaging laser scanners are transforming Hi-Level’s site surveys
One of the most important elements of a mezzanine floor project is the site survey, as this enables us to assess the site conditions first hand, take precise measurements and ensure our bespoke design fits the space.
We pride ourselves on our accuracy, so our recent investment in imaging laser scanners has got our surveyors and engineers quite excited! We caught up with Hi-Level surveyor Alasdair Reid to discuss how he surveys our sites and how this new technology is benefiting our customers.
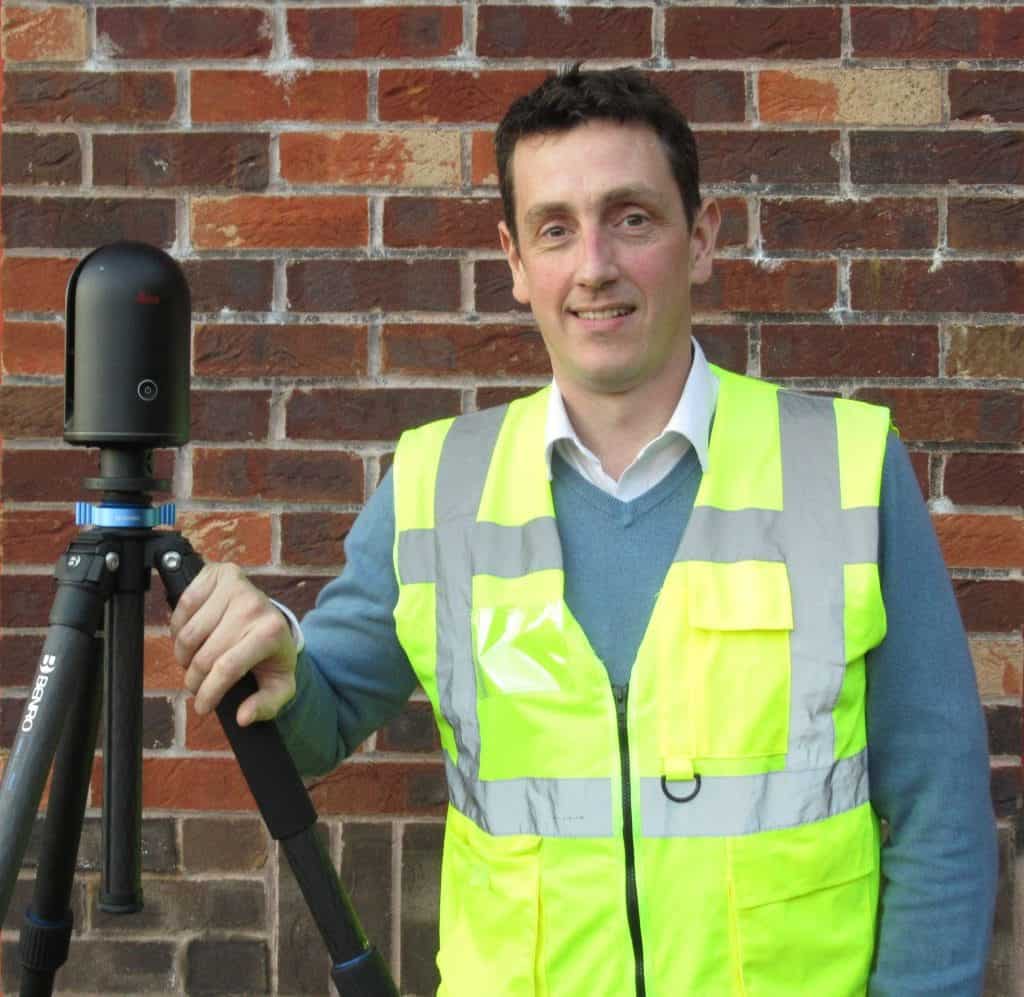
Talk us through what happens when you go to site. What are you looking for?
I collect a lot of information to help ensure the mezzanine floor is built precisely to fit the customer’s space. Firstly, I take measurements of the space where the mezzanine will be constructed to inform the design of the floor. I don’t just look at the floor space, I check for any potential obstructions or items that the floor needs to be built around.
I need to ensure all materials can be transported and erected safely within the area. I check the ceiling to ensure there are no obstructions hanging down and there will be at least 2 metre clearance from the top of the mezzanine stairs. Finally I check the level of the floor, using a laser level.
How does the imaging laser scanner work?
Once set up on the tripod, the scanner fires off hundreds of laser points in a 360 degree radius to capture everything (including me!) within about 10 metres, which returns a photographic-sharp image. This enables us to capture an extremely high level of detail and we can stitch together images to create a single 360 degree view of a site. It’s fast and very accurate, although I also use a hand-held laser scanner to double check dimensions to be completely belt and braces.
How the file is used back in the office?
The point clouds get imported in AutoCAD and from these our CAD technicians and structural detailers are able to create a highly accurate drawing for the customer. Office staff can pan around the whole premises virtually – we don’t need to return to site to check any details. The scan provides information that may have been missing from the initial customer enquiry, it enables us to understand the site better and spot any potential issues with down pipes etc that may affect the design of the floor. It’s particularly useful when the site has a lot of detail to capture, from cladding to braces which can be tricky to hand draw on a plan.
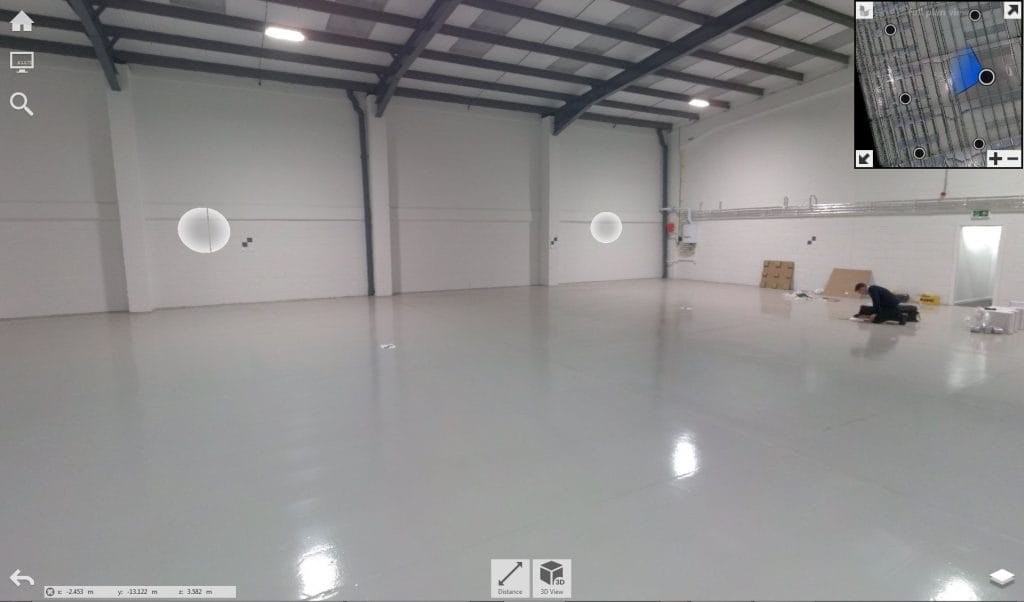
What are the benefits of using the imaging laser scanner?
Some companies design their floors based on customers’ floor plans, but at Hi-Level we prefer to always use ‘as built’ dimensions by visiting each site. Our surveys are far more accurate and we can assess the practicalities of our design when looking at a high resolution visual.
Another benefit to customers is time. Hand drawn site plans take longer to create and the imaging laser scanner can reduce our time on-site, meaning we can visit more customers more quickly to progress their projects. We also don’t need to take up so much of our customers’ time if they accompany us on-site, so it’s a win-win.