Mezzanines can be the answer to key market challenges facing the third-party logistics (3PL) warehouse industry.
The extra space and efficiencies a mezzanine provides are all the more relevant in the light of a landmark report into pressures facing the industry.
According to 3PL Central’s 2022 Benchmark Report, aggregating data from more than 200 3PL warehouses, major challenges include:
- Vacancy rates in warehousing at an all-time low
- Lease costs increasing
- Many warehouses operating above capacity and operational efficiency
- Labour shortages and labour costs leading to increased automation.
In each case, mezzanines can alleviate the pain, allowing 3PL professionals to make the most of their current premises without the expense and difficulty of renting more warehousing, and giving them more security in their operations and supply chains.
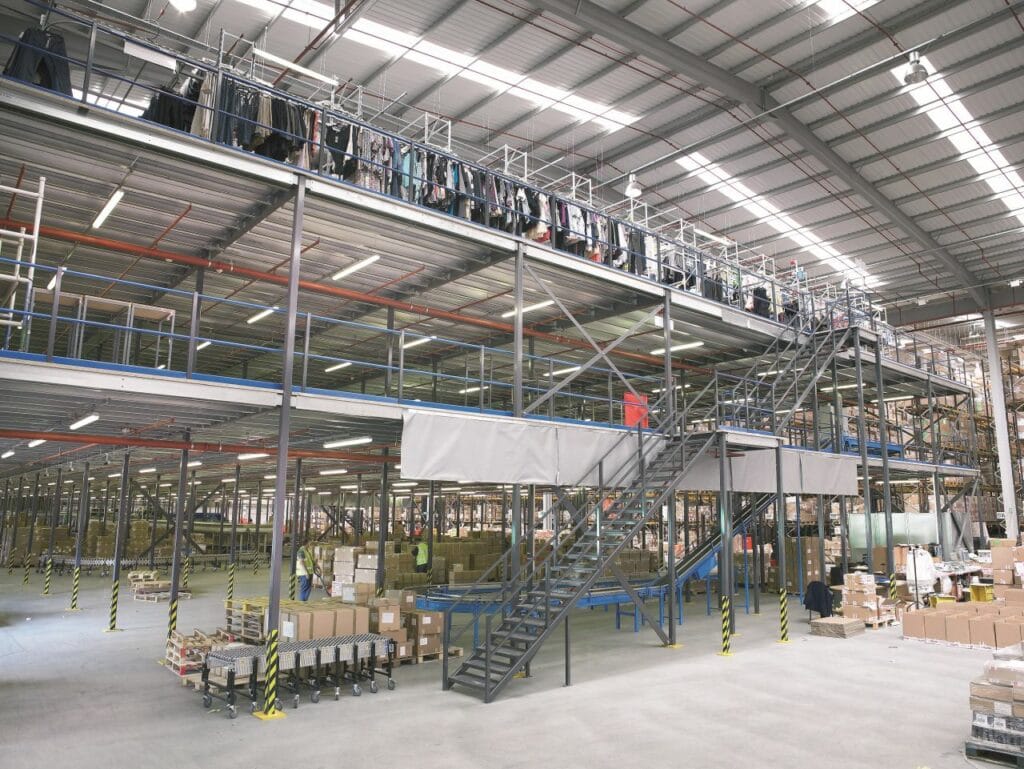
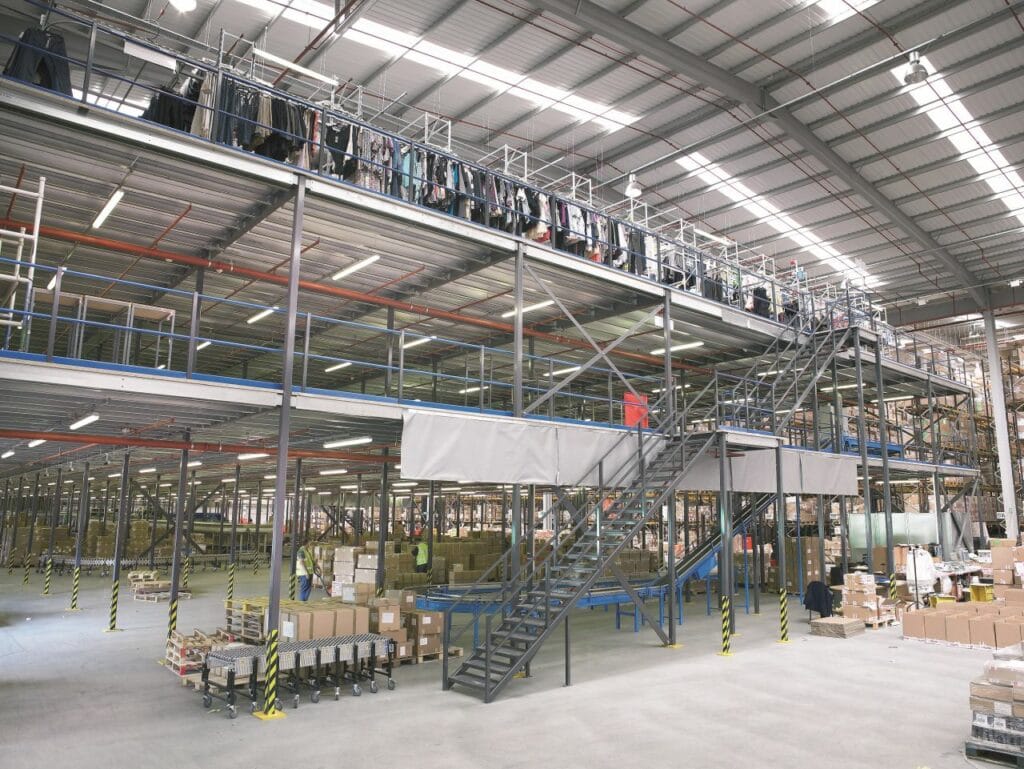
And with logistics firms increasingly investing in automation to store, manage and dispatch products, Hi-Level Mezzanines has developed a unique robot-ready flooring able to withstand the stringent demands of robotics.
Tackling space limitations
The report found many 3PLs are struggling to find new warehouse space or manage already-at-capacity existing footprints. Last year warehouse real estate approached record low vacancy rates and, compounded with increasing lease and purchase prices, one in five identified finding available warehouse space as one of their biggest headaches. Once they reach 80 to 85% space use, efficiency of movement and storage drops – and 15% said they are actually operating beyond 100%.
Hi-Level Mezzanines offers cost-effective solutions designed by our team of structural engineers. Mezzanines can be used for manufacturing, storage or as additional office and canteen space for new managers as production increases.
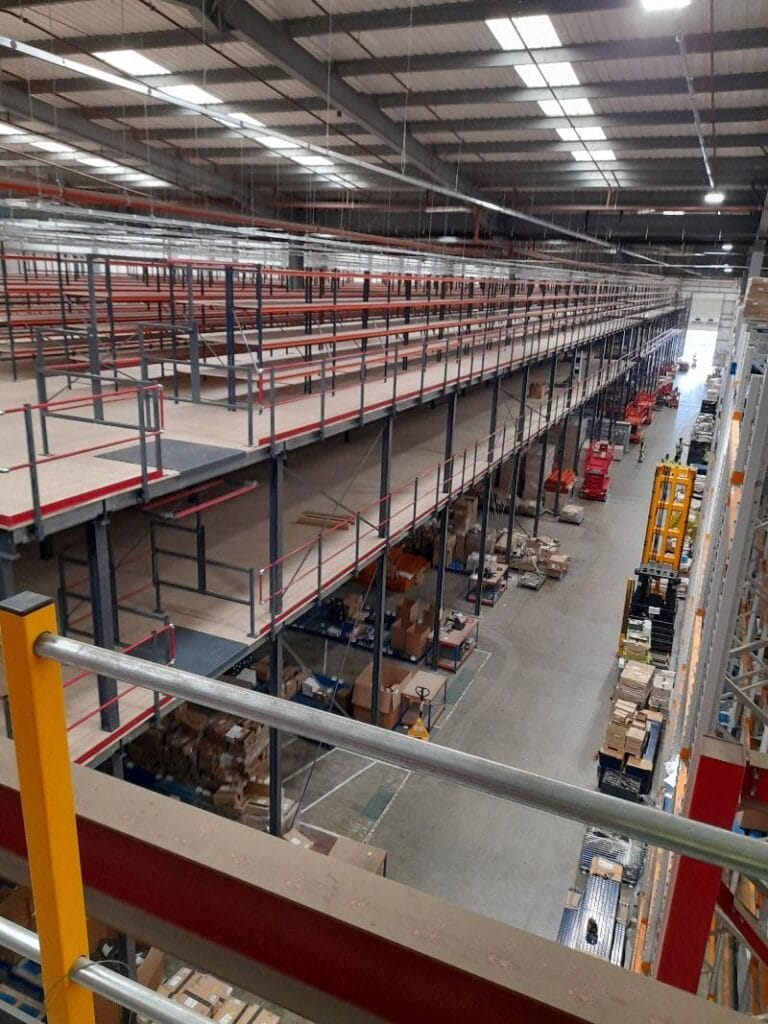
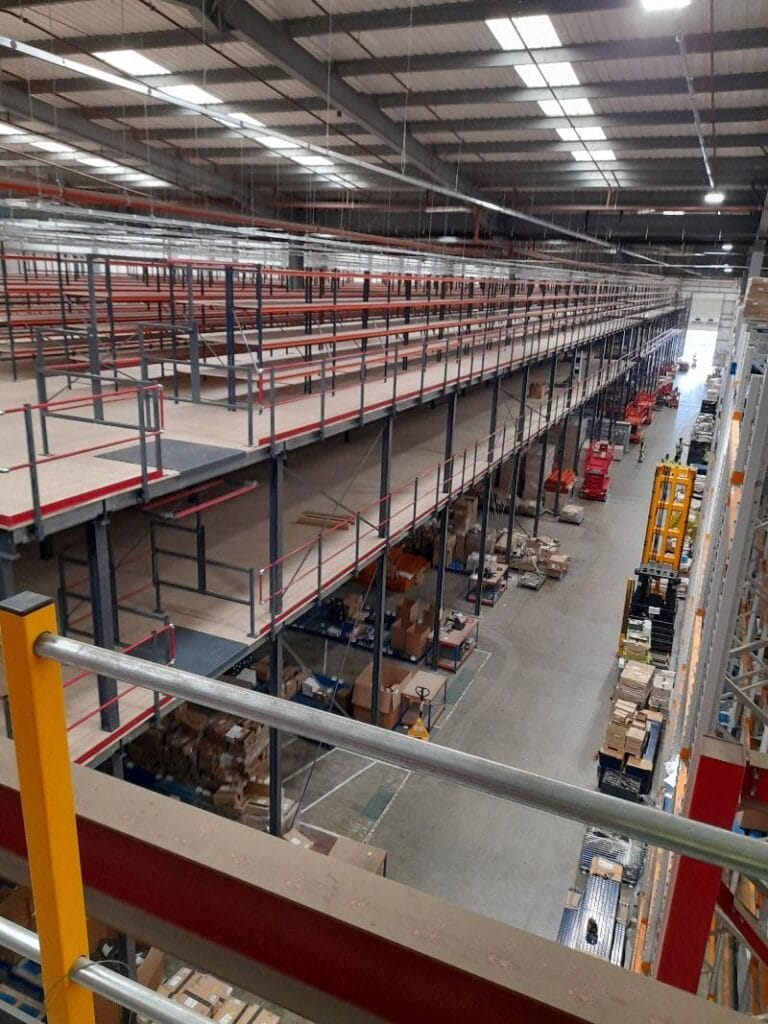
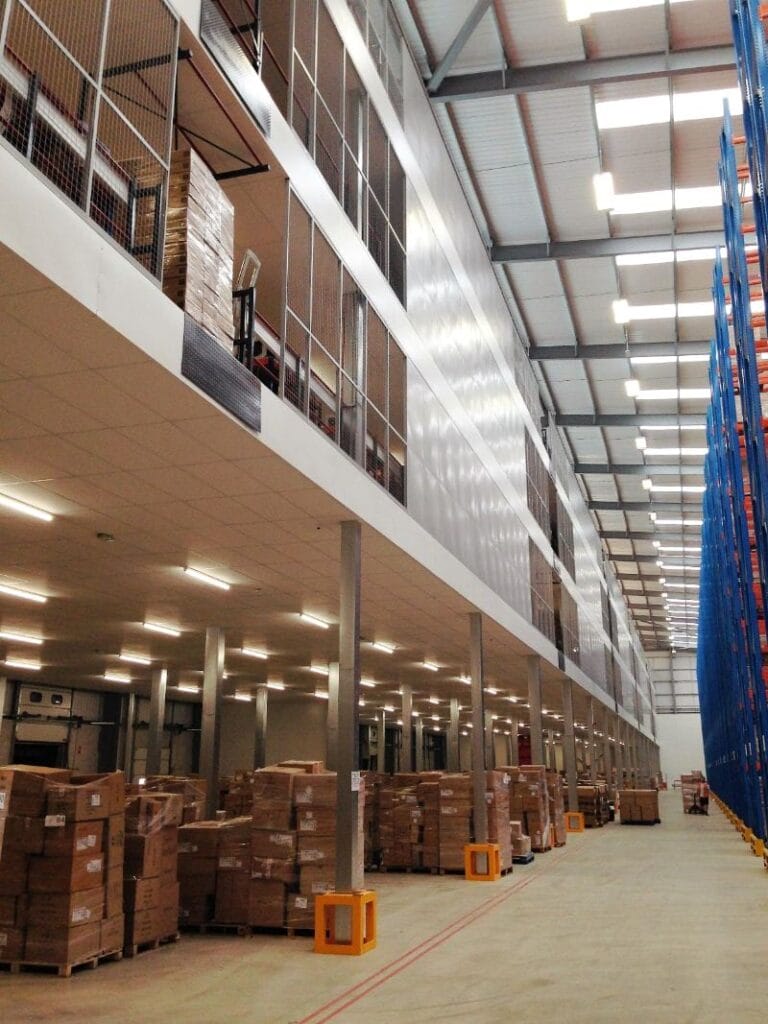
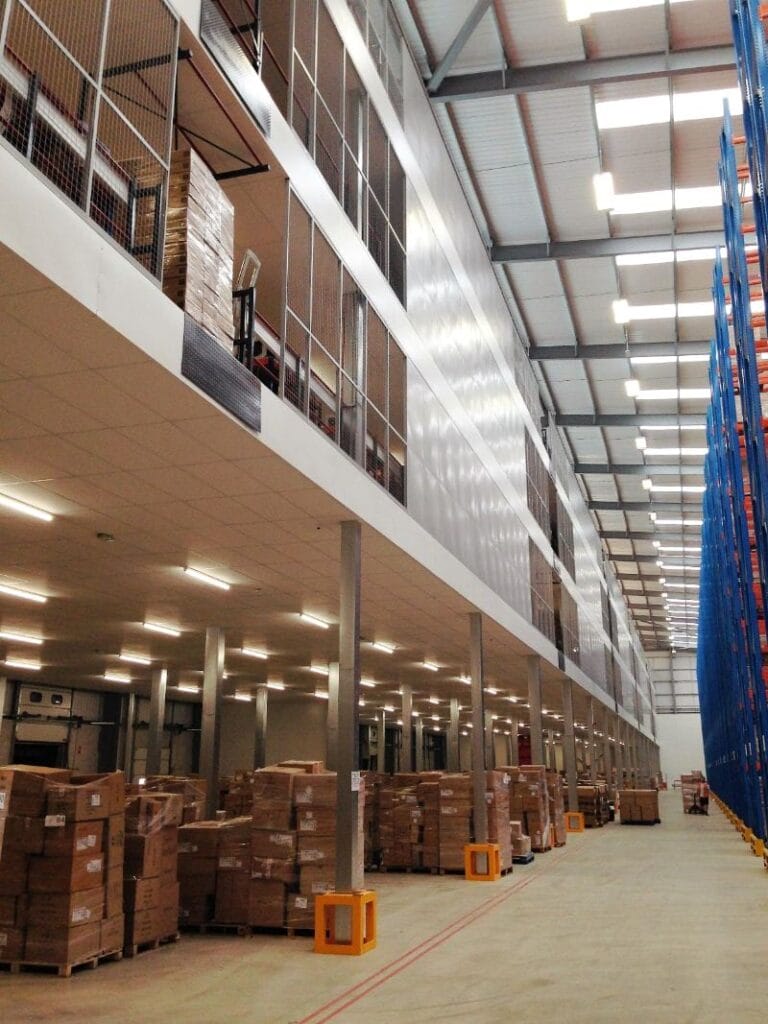
When one mezzanine is not enough, we have the skills to install multi-level mezzanines to maximise use of space: two to four tiers are usual, although we have installed five levels in one instance. For online retail giant ASOS, for example, we installed a three-tier mezzanine to create space for several new conveyor systems, provide additional storage and streamline the automation process inside its current distribution centre.
Another example is how our superbike clients GB Racing were at breaking point with an urgent need for more space for machinery and staff. A two-tier mezzanine has provided space for a production and processing area on the first floor, with storage on the second. Read our case study.
Tackling labour shortages and costs
Labour emerged as a considerable area of concern in the report, and many 3PL warehouses are looking to automation to address labour shortages and significantly higher labour costs. More than half said payroll makes up 40% or more of their total costs, and three quarters said labour costs have increased in the past year. It is no surprise, therefore, that half said their key to growth was automating warehouse processes.
This is where Hi-Level Mezzanines’ industry-leading robotic solutions add such value. Our new hybrid mezzanine flooring system consists of a robust interlocking 7mm textured PVC floor tile that can be fixed on top of 38mm particle board mezzanine decking. The panels have an anti-slip surface and are quick to install. They are exceptionally hard wearing to prevent indentations caused by robots running 24/7 along the same routes, as we have proved at an The Jewellery Channel (TJC) distribution centre in Feltham.
Retaining workers is another challenge, and another area where installing a mezzanine can help to solve the problem. Staying in current premises rather than moving to a new warehouse to expand capacity will both save money and help retain staff who might prefer not to travel to a different location. 3PLs can also benefit from the productivity advantages that come from an experienced workforce, as well as avoiding upheaval to their logistics planning.
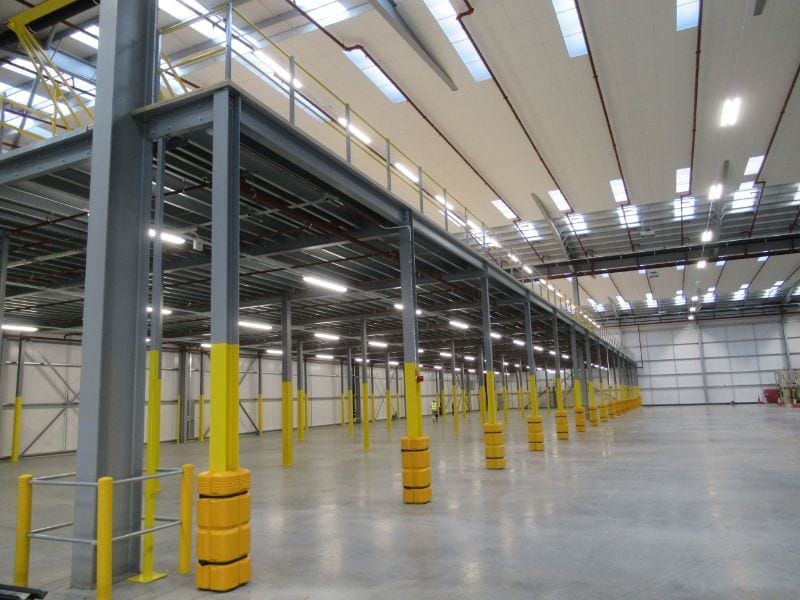
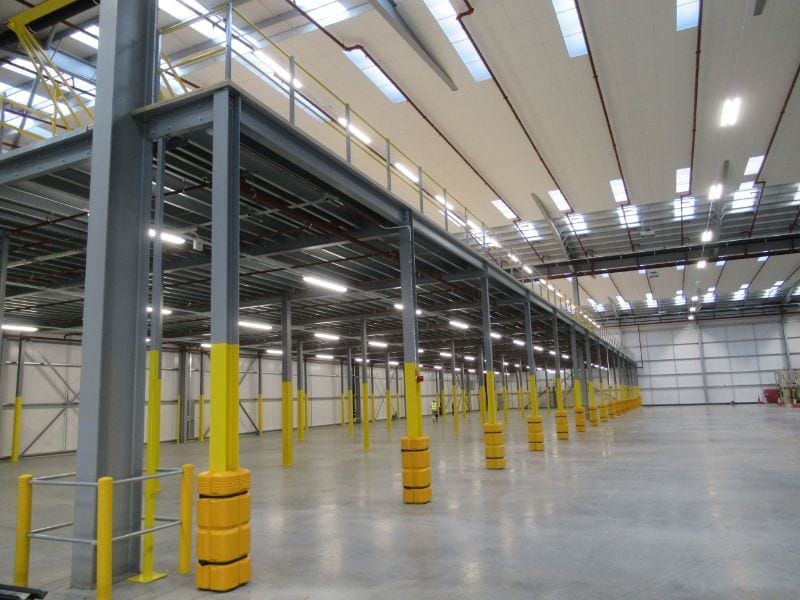
Looking ahead
These problems are unlikely to ease by themselves. The 3PL Central report highlighted a booming sector: soaring new customer acquisition and ecommerce ordering are very good news, but this growth will continue to lead to space and labour challenges. The threat of supply chain disruption is a further reason to install mezzanines to make use of all the capacity that 3PLs already have under their roofs.
As the report concluded: “This both an exciting and challenging time. Exciting because 3PLs overwhelmingly grew order volumes, profits and customers. Challenging because most were operating at or above warehouse capacity and could not find new space as a result of some of the lowest warehouse vacancy rates in history … Despite the challenging dynamics, they have thrived, innovated and diversified to support growth and harness the market opportunity.”
Hi-Level Mezzanines will be alongside them all the way.
Hi-Level Mezzanines provides mezzanine floors of the highest quality in the industry, yet remaining competitively priced thanks to the expertise of our team of qualified structural engineers, innovative digital design process and advanced solutions.
For 30 years we have been creating space for amazing things to happen. Contact us today for more information at [email protected] or call 01730 237 190.