The Client
GB Racing was founded in 2007 with over 100 years of engineering experience stemming from parent company Lewis Banks & Sons (Engineers) Ltd.
They manufacture secondary engine covers for the motorcycle industry selling both B2C and B2B in the UK. In addition, they sell their product all over the world to importers in South Korea, Indonesia, USA, Europe and many more.
GB Racing work with 90% of the World Superbike Paddock (World SBK) and have the only FIM approved engine protection product on the market. Since their founding in 2007 they have had 13 British Superbike champions (2009-2021), 9 World SBK champions (2013-2021) and 9 Moto2 champions (2012-2019, 2021).
The company is continuing to build on it’s success and growth by expanding their business into the marine industry and other areas of the motorcycle industry.
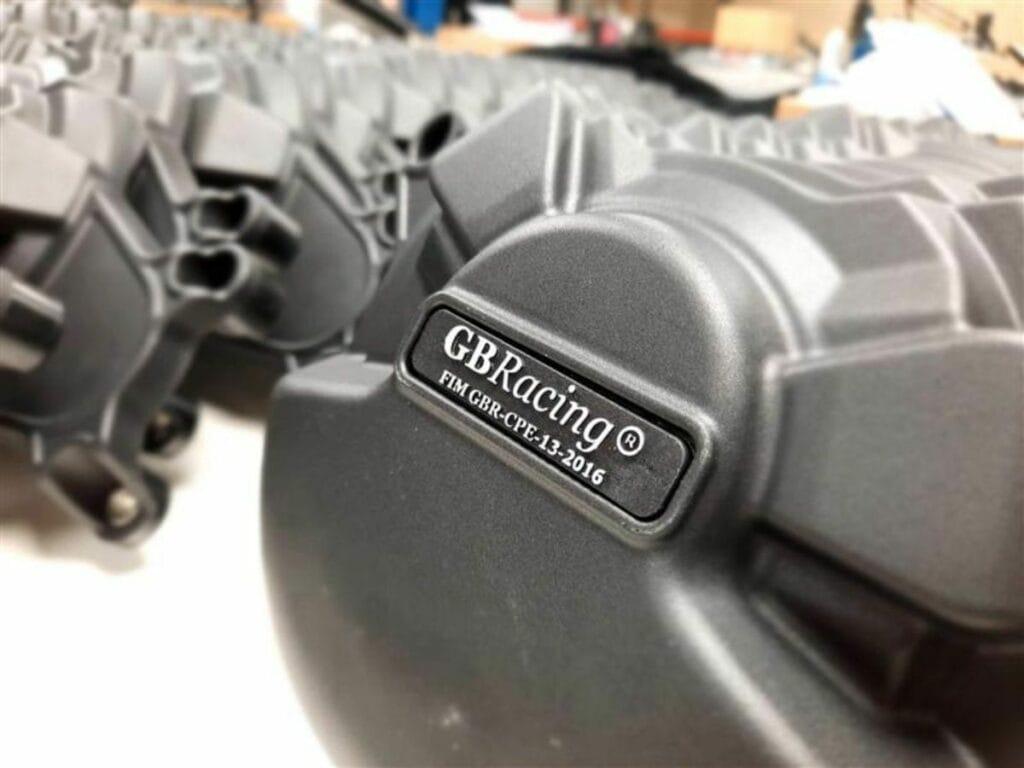
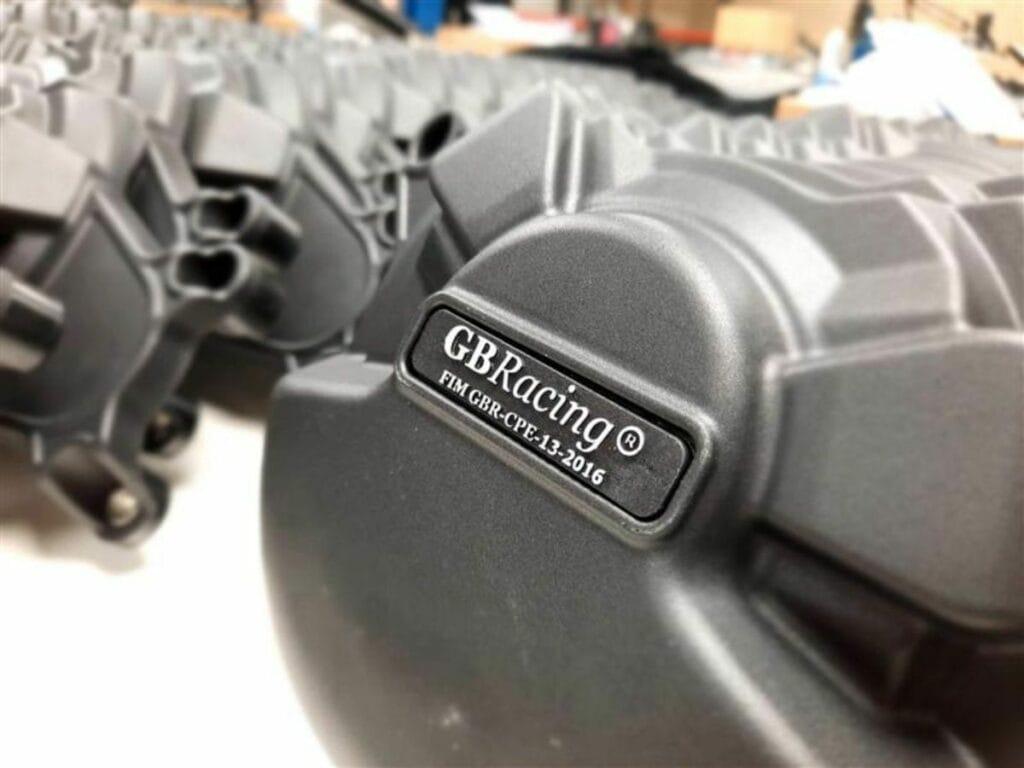
The Challenge
Due to company growth over previous years GB Racing needed to relocate to larger premises.
They found a new site in Hertfordshire in early 2021 and intended from the beginning to install a mezzanine as part of the new building to maximise the space available.
A key part of the mezzanine design was working round a 9 tonne milling machine located on the ground floor. This was the first thing in the new building and it was imperative that the mezzanine fitted around this.
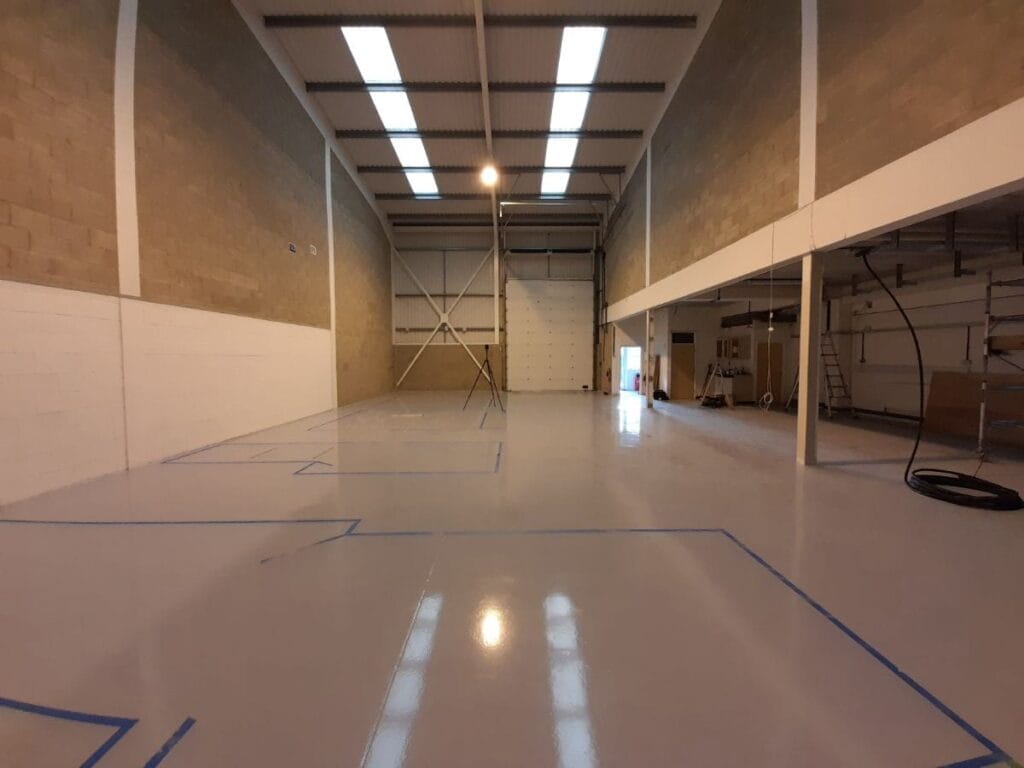
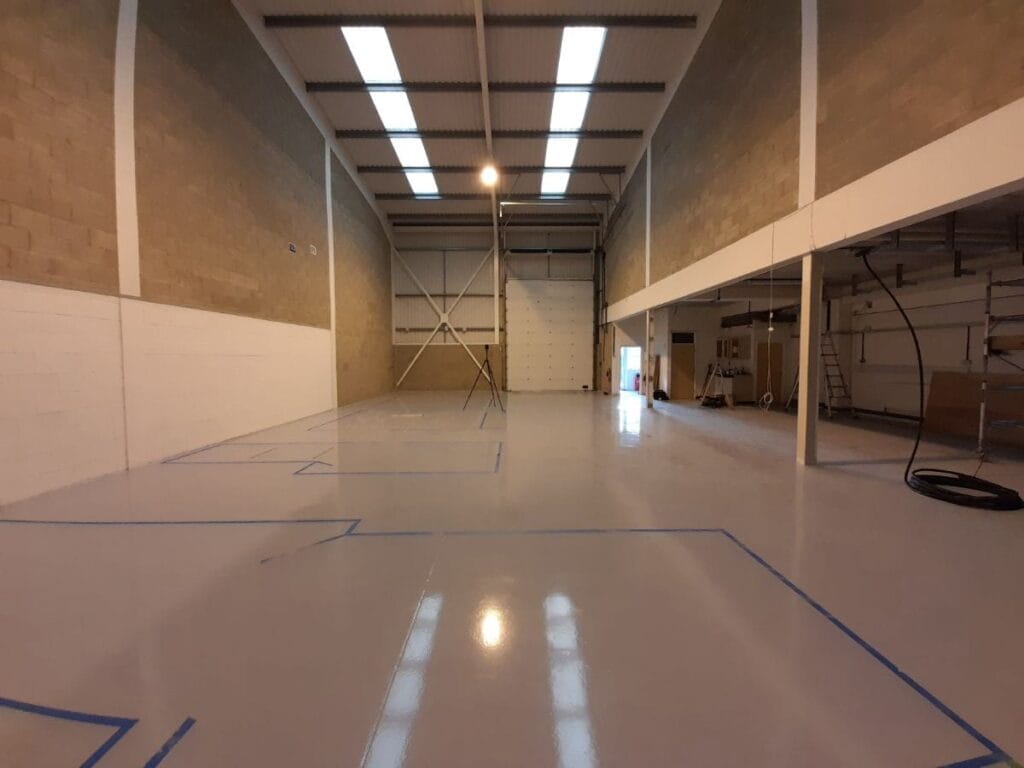
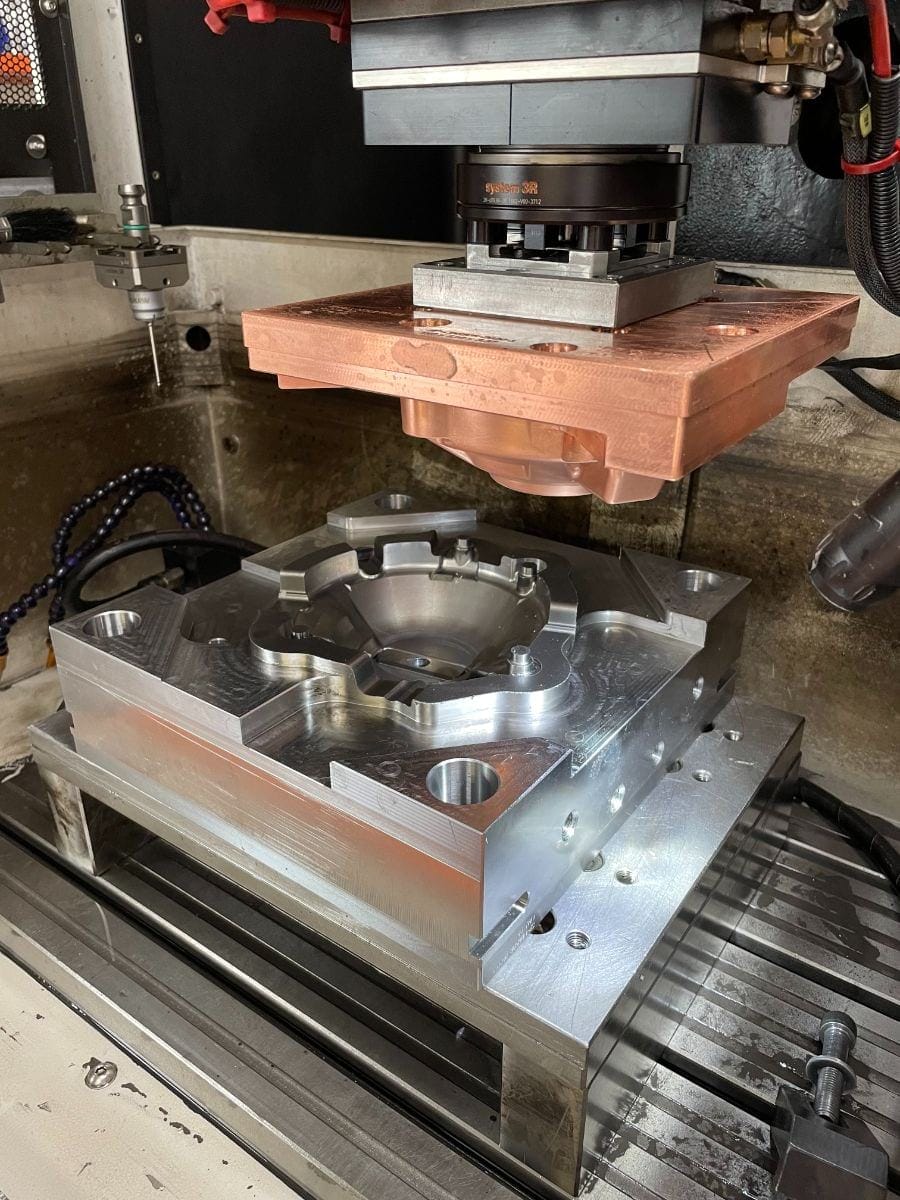
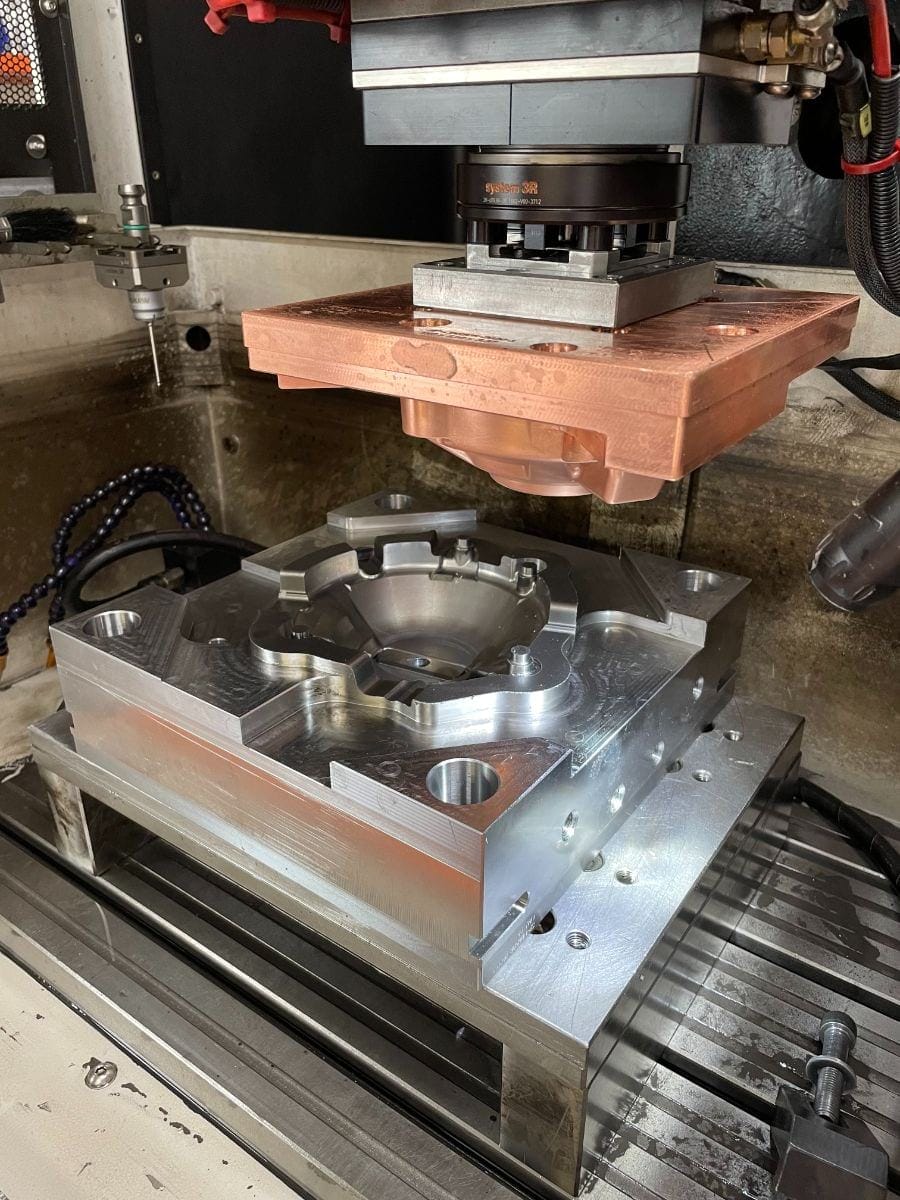
The Criteria
More space for product and additional staff as well as a better flow for product through the building.
To create a ground floor engineering workshop where both milling and injection moulding machine are located.
For product to be able to go from injection moulding machine up to second floor of mezzanine for storage.
For first floor of mezzanine to accommodate 7 new members of staff for production and dispatch of the finished product.
Specifications
Two-tier mezzanine – approx. 150m2 each tier.
2 x General access staircase
80m edge protection
Fire rating
The Result
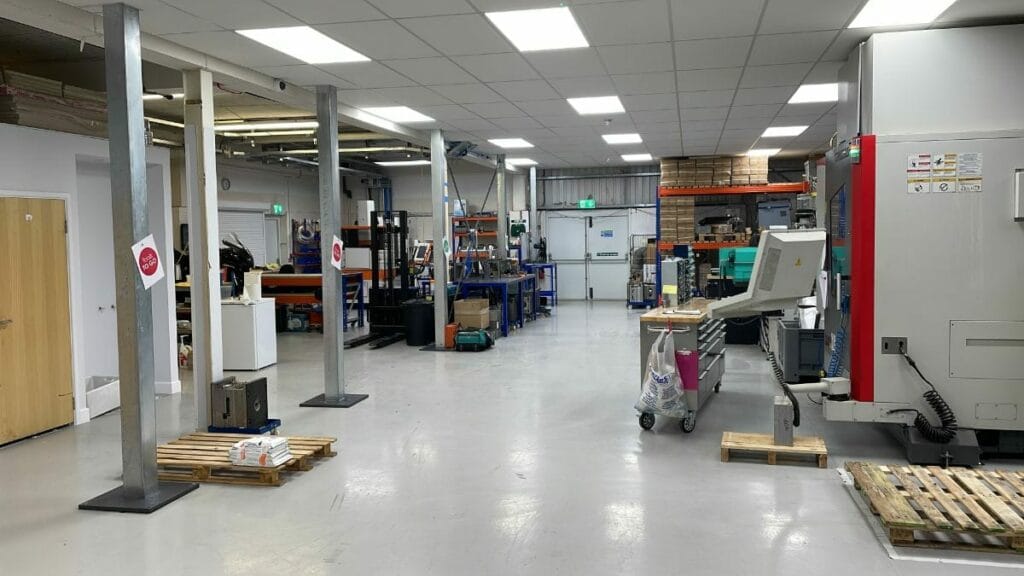
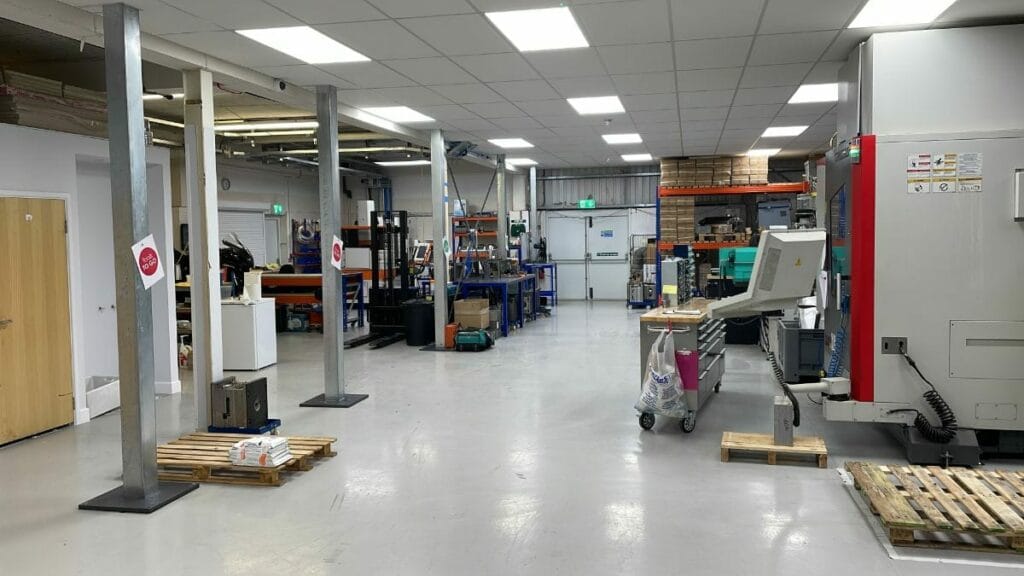
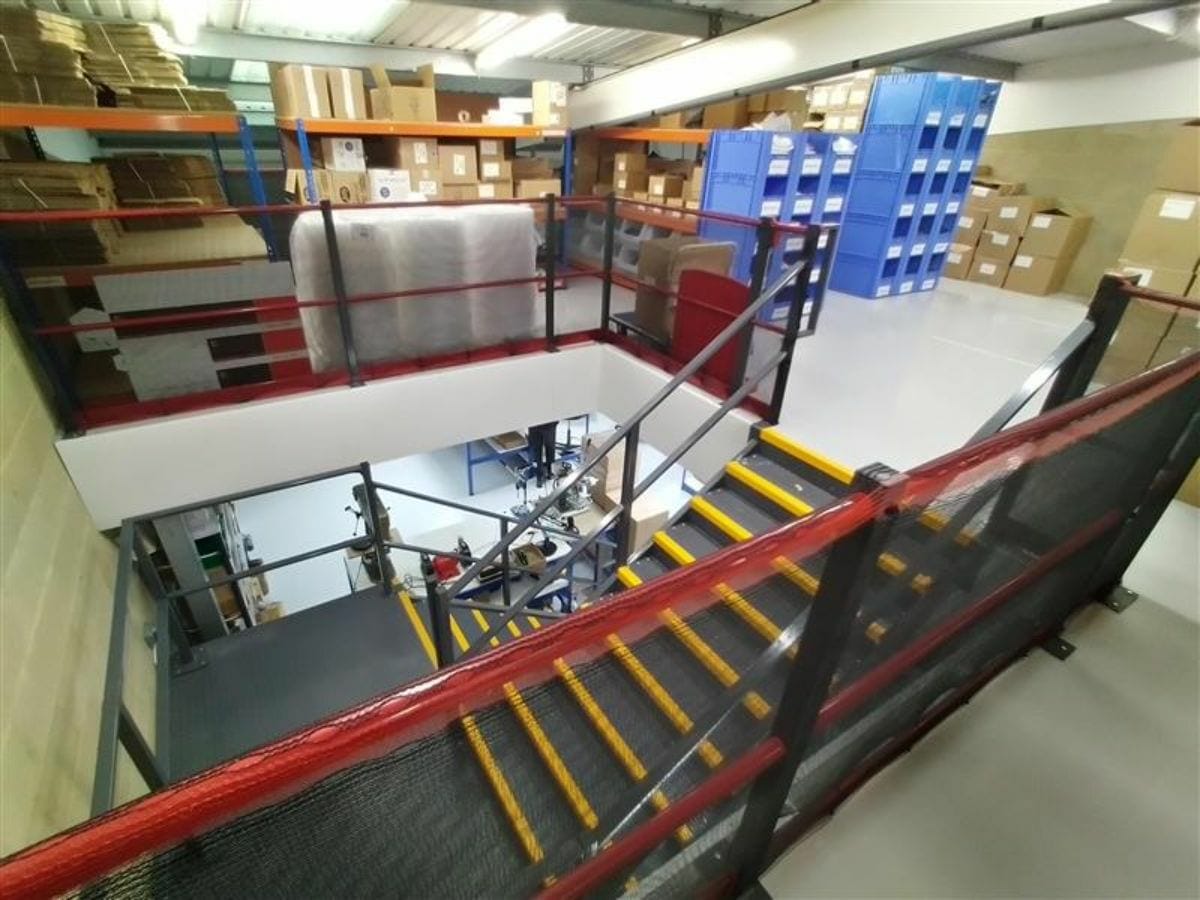
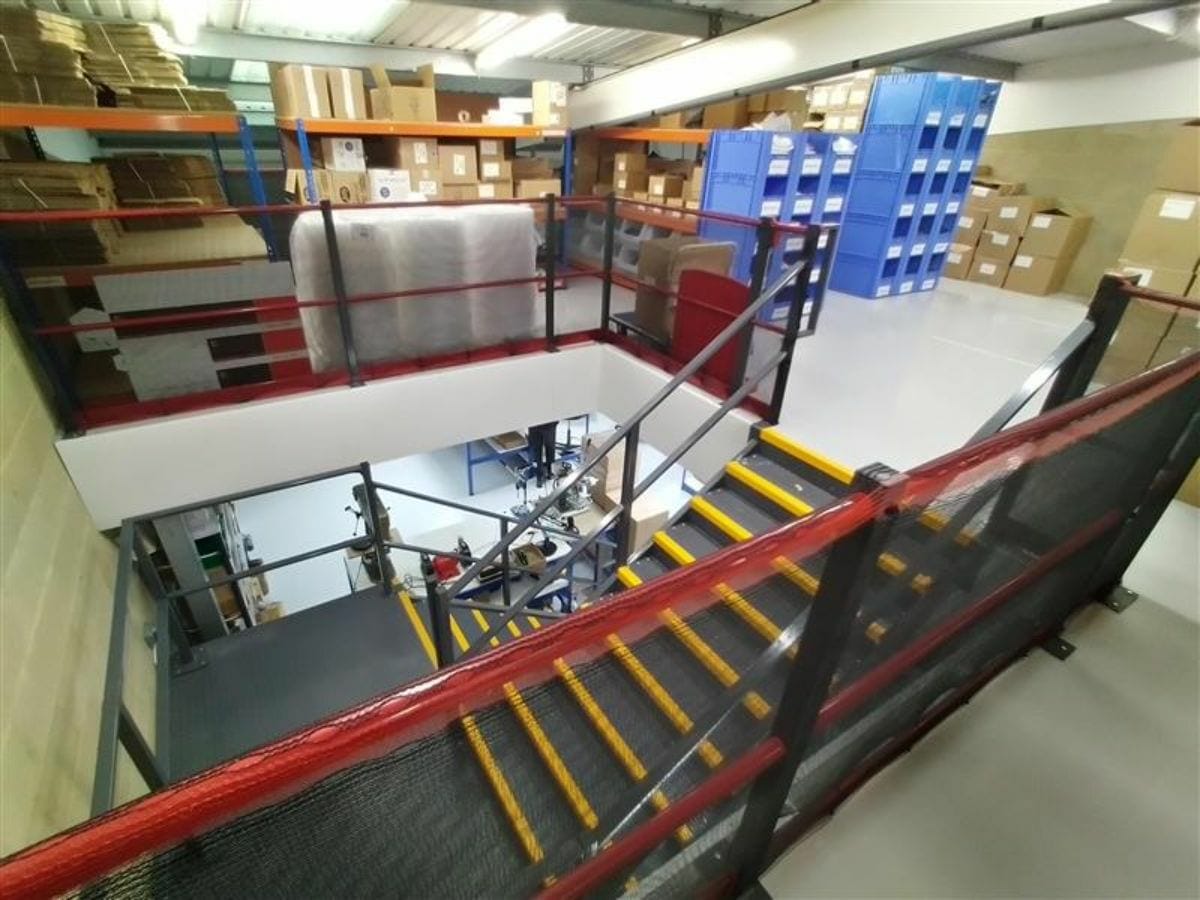
The new site has provided the space GB Racing need to allow for the business growth they have already experienced as well as planned expansion. With their injection moulding machine outputting up to 300 parts per day and new longer hours of operation now in place there is lots of potential for further growth.
Following a ground floor investigation survey, the Hi-Level project manager worked with GB Racing throughout the design process to ensure that the position of the mezzanine columns worked with the details in the survey report as well as around the large milling machine that was in situ.
The two-tier mezzanine has allowed for better flow of product through the various stages of the process as well as additional space for storage of product and work areas for new employees in the production/dispatch department. In addition, the mezzanine has allowed for safer and more efficient operations than the previous site with parts kept in racking being accessible from standing (without the use of ladders) and wider staircases for easy transport of packages between floors.
GB Racing moved into their new building in September 2021 and have been benefiting greatly from the additional space created by the mezzanine floor for the past 6 months.
Testimonial
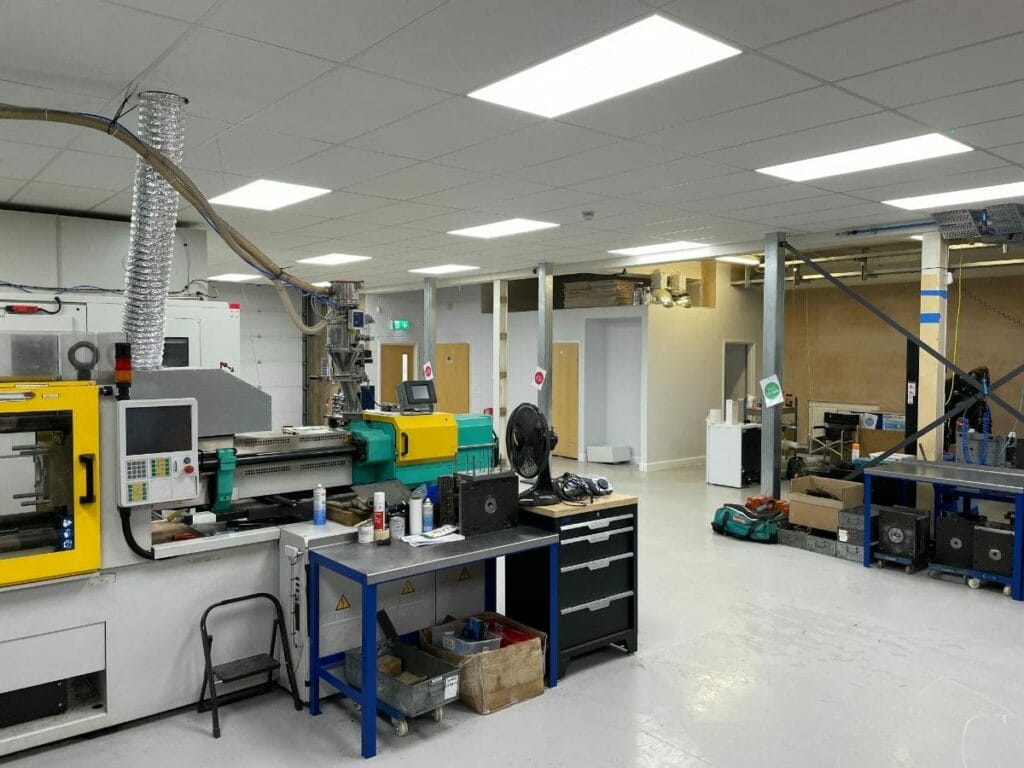
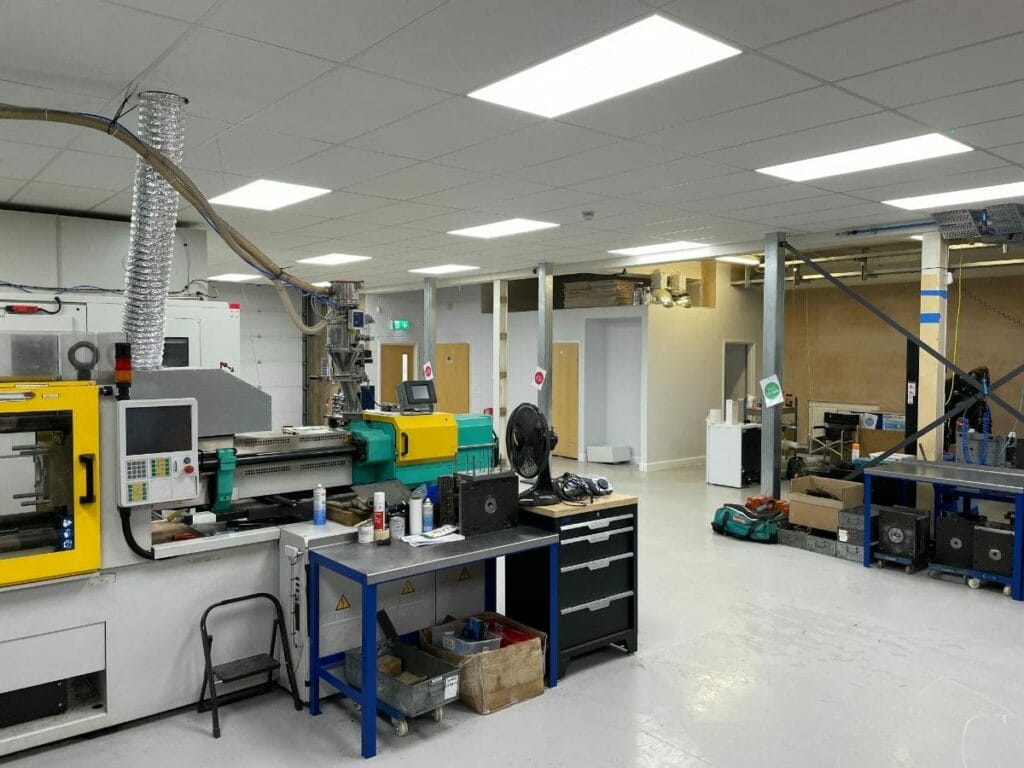
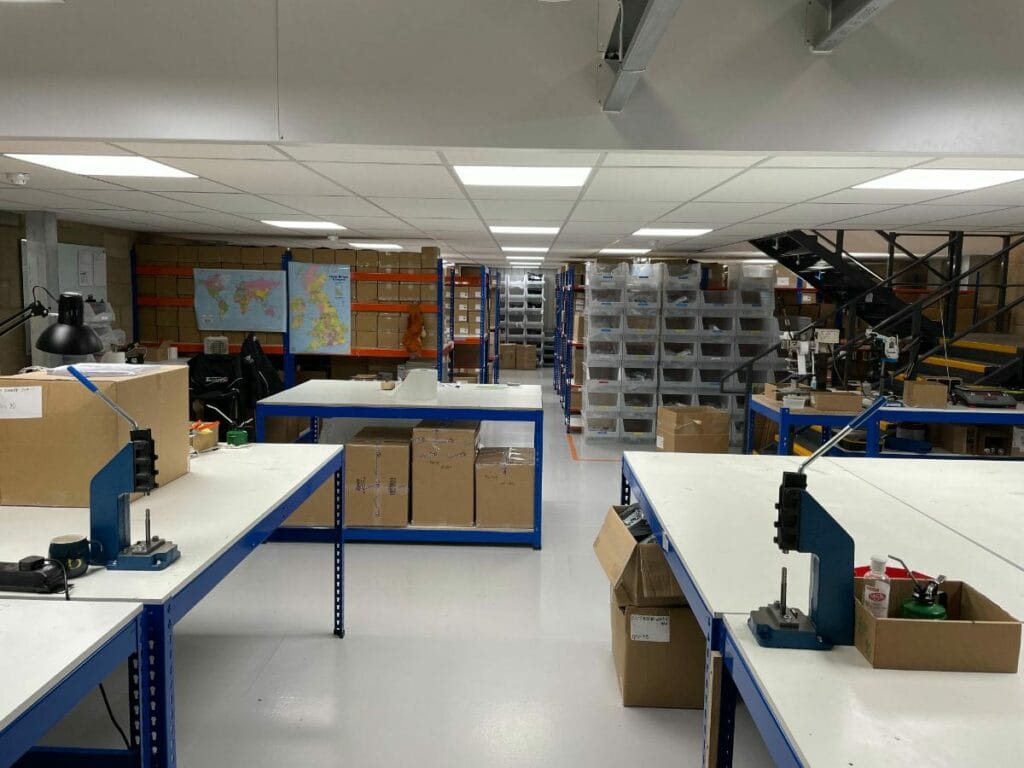
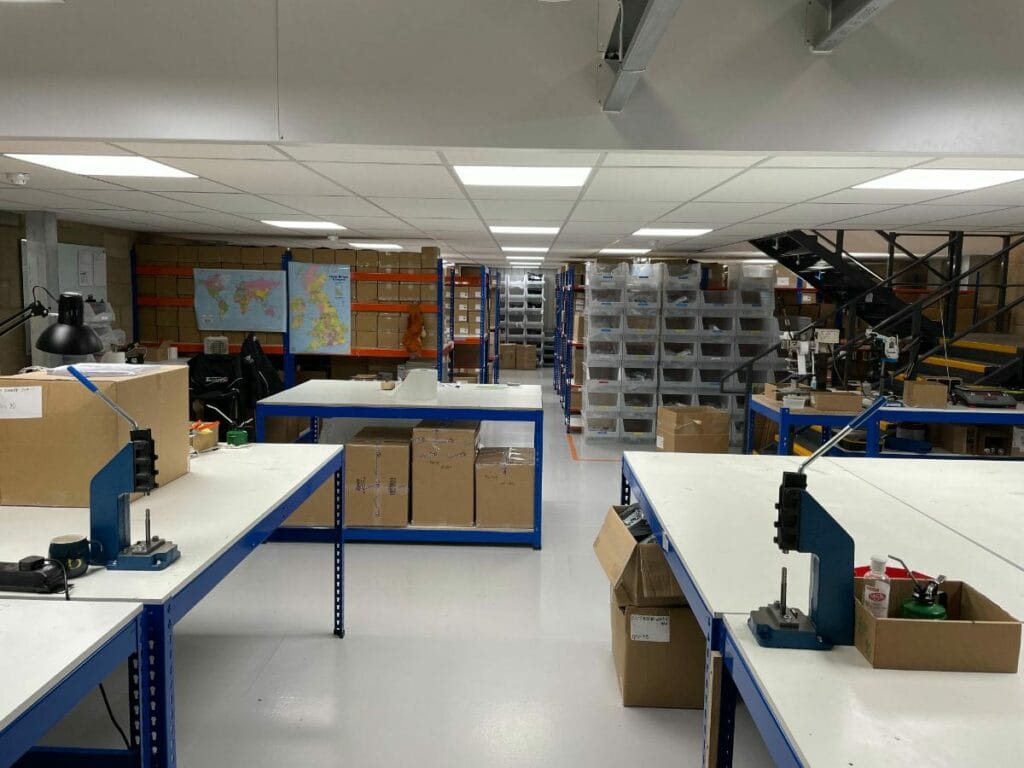
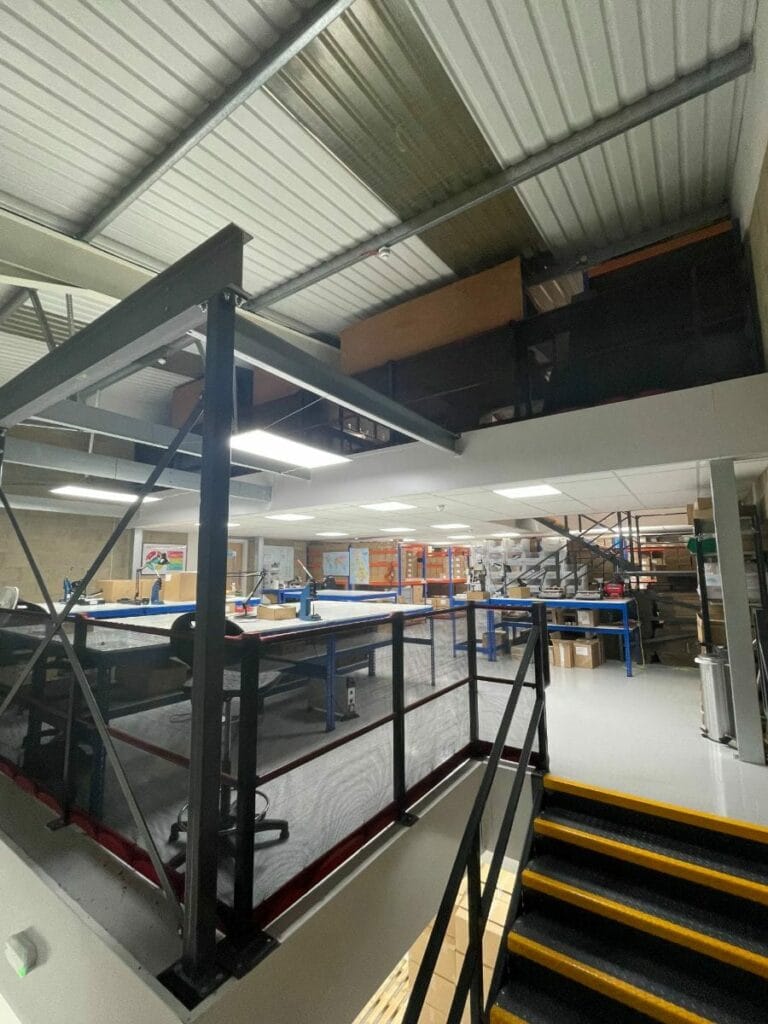
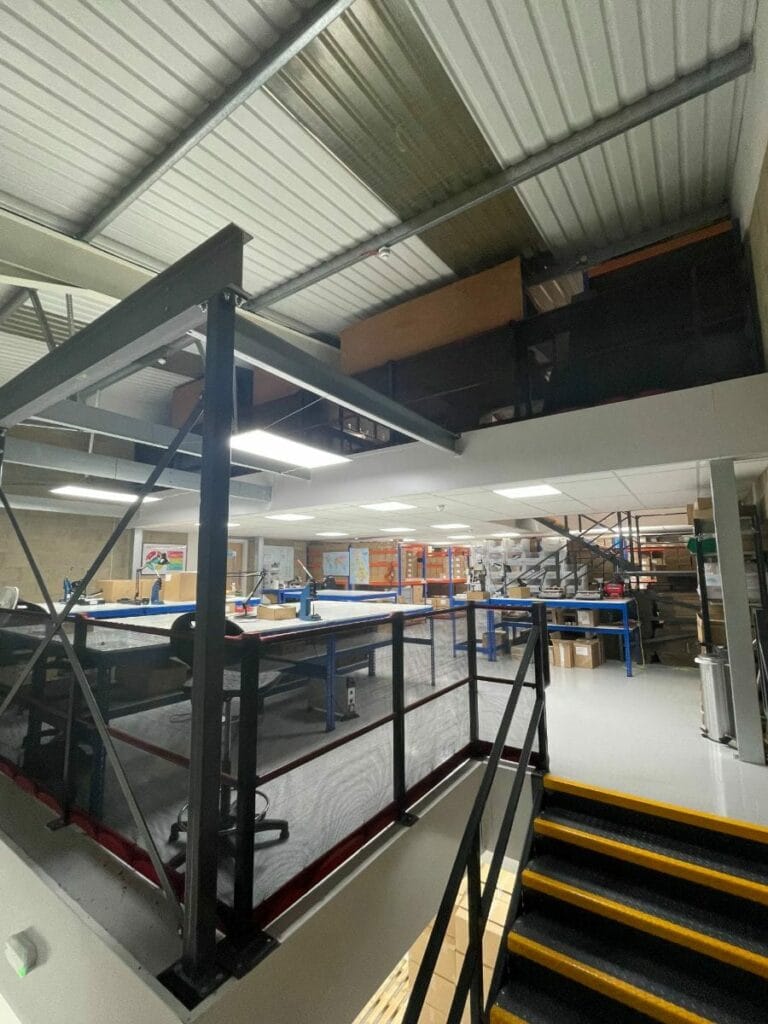
“Impressed with the scanning technology used at survey, the level of detail on drawings and the Project Manager’s technical assistance and guidance throughout the project. Even delays due to steel shortages caused by the Covid-19 pandemic were managed as well as possibly could be. Installation was fantastic – could not believe how quickly it happened!“